開発担当者のストーリー
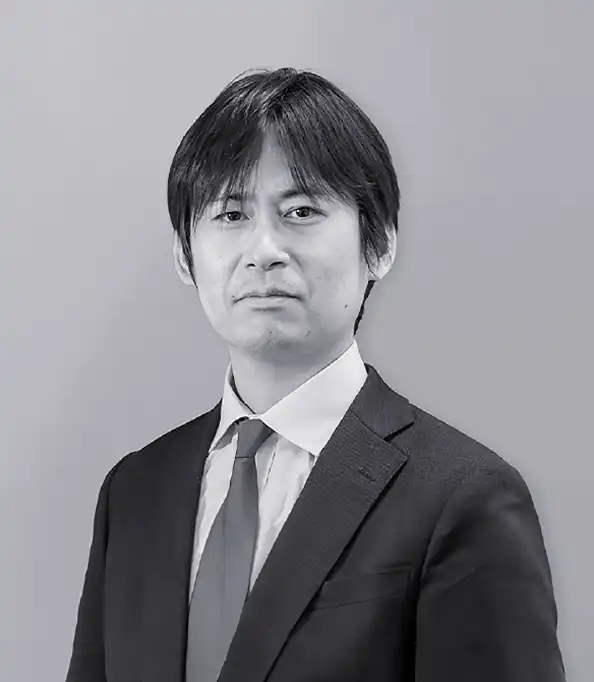
Tomoya Nakamura 執行役員 CKO 次世代事業本部 本部長
2008年、アクセンチュア株式会社の戦略グループに入社後、製造業クライアントの中期計画策定、新規市場参入戦略策定、営業改革、デジタルトランスフォーメーションなど幅広いプロジェクトを経験。2017年、株式会社TBMに入社し、海外展開や用途開発などに携わる。2018年、Bioworks株式会社のグループ化に関わり、取締役に就任。 2021年、SKグループとの資本業務提携に関わり、SKグループとの合弁会社であるSK TBMGEOSTONEの取締役に就任。
CCU技術の普及に向けた挑戦
この度、排ガス中のCO₂を回収し、原料として使う次世代LIMEXの開発に目途がつけられたことをとても嬉しく思います。
人口の増加、途上国の経済発展と脱炭素を両立するには、CO₂の排出量を減らすのみならず、排出されたCO₂を吸収して再利用することは不可欠であり、IEAの試算では、エネルギーセクターで2070年にカーボンニュートラルを実現するには、CCUSが約19%を担わなければなりません。
しかしながら、私たちは2070年まで待てるわけではありません。経済産業省のカーボンリサイクルロードマップでも、CCU技術を使った製品の普及は2030年頃からとなっていますが、私たちはそれを前倒しして、少しでも早くCCU技術を使った製品を社会に広めるべく挑戦して参りました。
CO₂を原料にして作る、炭酸カルシウムを含む炭酸塩は、その技術や品質の課題から、用途としてコンクリートやセメント原料がメインで考えられていましたが、コストがなかなか合いませんでした。次世代LIMEXは、この炭酸カルシウムの高付加価値な出口であり、サステナビリティ領域のトッププレーヤーを目指す私たちが先頭に立って、次世代LIMEXで、CCU技術の普及を担う責任があると感じています。
我が国のGX実現に向けた基本方針においても、TBMからのパブリックコメントの内容が認められ、CO₂削減コンクリート等のセクションに、炭酸カルシウム製品等の導入支援・需要喚起策を追記して頂くことができました。
私たちの挑戦は始まったばかりですが、応援して下さる国や自治体、多くの企業の皆様のご期待に応え、CCU技術の普及に邁進してまいりますので、引き続き応援の程、よろしくお願いいたします。
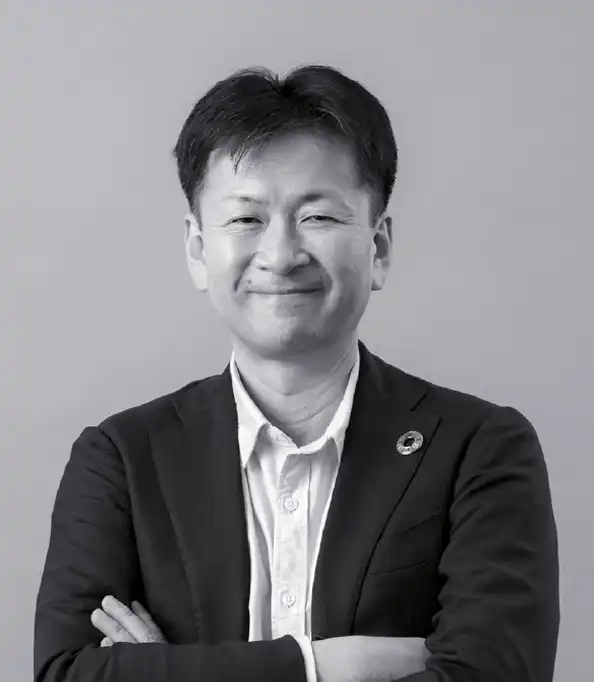
Yorinobu Takamatsu テクノロジーセンター センター長
早稲田大学院卒業後、スリーエムジャパン株式会社にて高分子技術の研究開発に従事、Senior Specialist(Technical Ladder)という役職に就く。アクリルポリマーを主体とした接着・粘着剤の分子設計及び重合技術について研究開発、製造技術への応用業務に従事。日本国内で108件の特許出願(国際出願54件)、43件の特許取得、さまざまな製品を立ち上げ、年間200億円ほどの売り上げに貢献。2021年、TBMに入社。TBMの技術の根幹となるテクノロジーセンターにてLIMEXやCirculeXの様々な用途に適したコンパウンド材料の開発、機能性の付与、新製品の開発など、材料開発業務全般に携わる。
技術ノウハウを結集した、次世代LIMEXの開発
弊社技術拠点であるテクノロジーセンターのセンター長として、LIMEXのさまざまな用途への展開を推進しております。TBMの根幹技術は、炭酸カルシウムを代表とした無機フィラーを50%以上樹脂に均一に充填するための混錬技術および、既存の成型(射出・押出・ブロー・インフレーション・真空など)に適応するための配合技術・成形技術です。
CCU技術により得られる炭酸カルシウムと、現在主に使用している重質炭酸カルシウムは、似て非なるものであり、その生成機構の理解、性状の違いを明確化し、今まで蓄積してきた技術ノウハウを結集し、次世代LIMEXへと展開しております。身の回りのあらゆる物がLIMEXとなるよう、浸透させていきたいです。
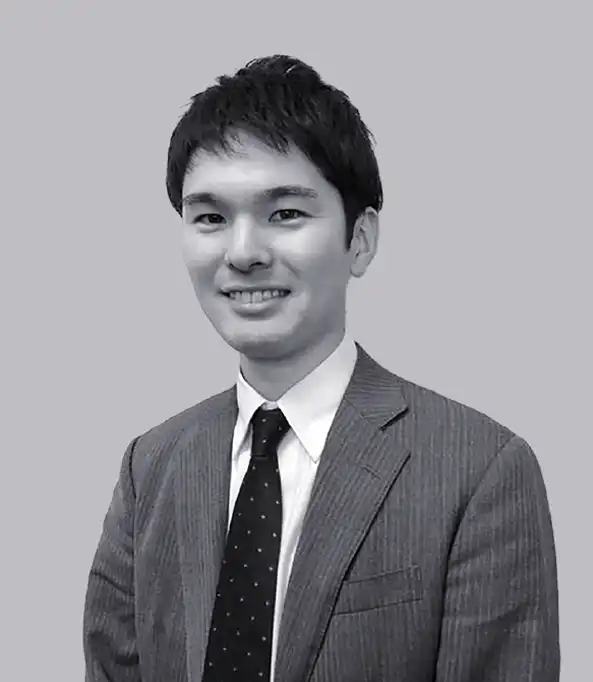
Kenshi Takahashi 次世代事業本部 / 生産技術部
東北大学大学院環境科学研究科修了後、三菱マテリアル株式会社に入社。廃棄物のリサイクルプロセス開発に従事するとともに、新工場の立ち上げ支援を経験。2021年、株式会社TBMに入社。東北LIMEX工場の立ち上げや生産工程改善に従事するとともに、CR LIMEXの実現に向けた技術開発を推進。
次世代LIMEXのポテンシャルの具現化に向けて
大学時代から一貫して環境・リサイクルの課題解決に取り組んできました。30歳を迎えるにあたって新たな挑戦を求めていた中で、LIMEXに出会い、その革新的なコンセプトに加え、カーボンリサイクル技術の活用で環境性能を更に向上できるポテンシャルに大きな魅力を感じて、TBMにジョインしました。
次世代LIMEXに関する技術開発は2021年4月頃からスタートしました。しかし当時は、社内の研究環境は十分に整っておらず、具体的にどうやって研究を行うのか、リソースが限られる中でどう効率よく進めていくか、というところから考えていく必要がありました。そんな中、接点のあった東北大学の先生にご協力をいただきながら少しずつ技術検証を進め、同大学との共同研究に発展。さらにはNEDO助成事業に採択され、開発を加速。様々な苦労をしながらも、短期間で製品化の目途をつけることができたと思っています。
一方で、社会実装に向けた課題はまだまだあります。また、カーボンリサイクルで作る炭酸カルシウムには、環境性能の向上だけでなく、様々な機能を付与できる可能性があります。この大きなポテンシャルの具現化に今後も尽力していきたいと思います。